H13 Hot Work Tool Steel Description
H13 die steel for the manufacture of large impact load die, hot extrusion die, fine forging die; Die casting moulds for aluminum, copper and its alloys.
Name: H13 die steel
Execution standard: GB/T1299-2000
Uniform digital code: T23353
Class type: Hot work die steel
H13 Hot Work Tool Steel Introduction
H13 is hot work die steel, according to the standard GB/T1299 — 2000. ; Number 4cr5MoSiV1; Alloy tool steels, referred to as composite steel, are steels formed by adding alloying elements on the basis of carbon working steel. The working steel includes: measuring tool steel, impact resistant tool steel, cold work die steel, hot work die steel, non-magnetic die steel, plastic die steel.
Chemical Component
ASTM A681 | C | Mn | P | S | Si | Cr | V | Mo | ||||||
H13 | 0.32 | 0.45 | 0.2 | 0.6 | 0.03 | 0.03 | 0.8 | 1.25 | 4.75 | 5.5 | 0.8 | 1.2 | 1.1 | 1.75 |
DIN ISO 4957 | C | Mn | P | S | Si | Cr | V | Mo | ||||||
1.2344 /X40CrMoV5-1 | 0.35 | 0.42 | 0.25 | 0.5 | 0.03 | 0.02 | 0.8 | 1.2 | 4.8 | 5.5 | 0.85 | 1.15 | 1.1 | 1.5 |
JIS G4404 | C | Mn | P | S | Si | Cr | V | Mo | ||||||
SKD61 | 0.35 | 0.42 | 0.25 | 0.5 | 0.03 | 0.02 | 0.8 | 1.2 | 4.8 | 5.5 | 0.8 | 1.15 | 1.0 | 1.5 |
Application of AISI H13 Tool Steel
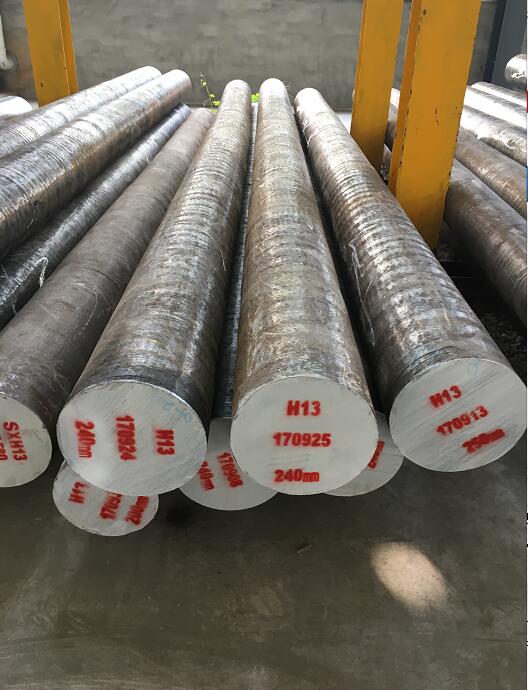
H13 die steel for the manufacture of large impact load die, hot extrusion die, fine forging die; Die casting moulds for aluminum, copper and its alloys.
H13 air quenched hot work die steel imported from USA. Its performance, use and 4Cr5MoSiV steel are basically the same, but because of its high vanadium content, so the performance of the medium temperature (600 degrees) is better than 4Cr5MoSiV steel, is a representative steel in the hot work die steel is widely used.
H13 SIZE
- H13 Steel Round Bar: diameter 8mm – 400mm
- H13 Steel Plate: thickness 16mm –500mm x width 200mm – 800mm
- H13 Steel Slab: 200mm x 500-800mm
- H13 die steel plate width (210-610) * thickness (6-80) hot rolled
- H13 Mold Steel Tube Outer Diameter (6-219) * Wall Thickness (0.5-25)
- H13 mould steel ingot electroslag ingot 0.35t 0.5t 0.75t 1.0t 1.5T 1.8T 2.0T 2.5T 2.8T (3.0-8.0) T
H13 Steel Mechanical Properties
Properties | Metric | Imperial |
Tensile strength, ultimate (@20°C/68°F, varies with heat treatment) | 1200 – 1590 MPa | 174000 – 231000 psi |
Tensile strength, yield (@20°C/68°F, varies with heat treatment) | 1000 – 1380 MPa | 145000 – 200000 psi |
Reduction of area (@20°C/68°F) | 50.00% | 50.00% |
Modulus of elasticity (@20°C/68°F) | 215 GPa | 31200 ksi |
Poisson’s ratio | 0.27-0.30 | 0.27-0.30 |
Application of AISI H13 Tool Steel
- As Tools for Extrusion
Part | Aluminium, magnesium alloys, HRC | Copper alloys HRC | Stainless steel HRC |
Dies, Backers, die-holders, liners, dummy blocks, stems | 44-50 | 43-47 | 45-50 |
41-50 | 40-48 | 40-48 | |
Austenitizing temperature | 1,870-1,885°F | 1,900-1,920°F | |
(1,020-1,030°C) | (1,040-1,050°C) |
As Plastic Molding Tool Steel
Part | Austenitizing temp. | HRC |
Injection molds Compression/ transfer molds | 1,870-1,885°F (1,020-1,030°C) | 50-52 |
Tempering 480°F (250°C) |
- Other Applications
Applications | Austenitizing temp | HRC |
Severe cold punching, scrap shears | 1,870-1,885°F | 50-52 |
(1,020-1,030°C) | ||
Tempering 480°F (250°C) | ||
Hot shearing | 1,870-1,885°F | |
(1,020-1,030°C) | 50-52 | |
Tempering 480°F (250°C) or | ||
1,070-1,110°F | 45-50 | |
(575-600°C) | ||
Shrink rings (e.g. for cemented carbide dies) | 1,870-1,885°F | 45-50 |
(1,020-1,030°C) | ||
Tempering 1,070-1,110°F | ||
(575–600°C) | ||
Wear-resisting parts | 1,870-1,885°F | Core 50-52 Surface ~1000HV1 |
(1,020-1,030°C) | ||
Tempering 1,070°F (575°C) | ||
nitrided |
If there are any queries about AISI H13 tool steel for hot working applications, please feel free to leave a comment below. And welcome enquiry of AISI H13 tool steel, Lion Metal are professional and reliable supplier for prime H13 tool steel materials.
H13 Hot Work Tool Steel Properties
Electroslag remelting steel, the steel has high hardenability and thermal crack resistance, the contain higher content of carbon steel and vanadium, good wear resistance, toughness is relatively less, has good heat resistance, high temperature has good strength and hardness, high wear resistance and toughness, excellent comprehensive mechanical properties and high resistance to tempering stability.
H13 Hot Work Tool Steel Hardness Analysis
The carbon content in the steel determines the matrix hardness of the hardened steel. According to the relationship curve between the carbon content in the steel and the hardness of the hardened steel, the quenching hardness of H13 die steel is about 55HRC.
For tool steels, part of the carbon in the steel enters the steel matrix and causes solution strengthening. The other part of the carbon will combine with the carbide forming element of the alloying element to form the alloying carbide. For hot work die steels, besides a small amount of the alloy carbide remains, it is also required that it disperses and precipitates on the quenched martensite matrix to produce two hardening phenomena during the tempering process.
Thus the properties of hot work die steels are determined by the uniform distribution of residual alloying carbon compounds and the microstructure of tempered martensite. Thus, the content of C in steel should not be too low.
Heat Treatment for H13 Tool Steels
Annealing
Heat slowly to 1550°-1650°F, hold until entire mass is heated through, and cool slowly in the furnace (40F per hour) to about 1000°F, after which cooling rate may be increased. Suitable precautions must be taken to prevent excessive carburization or decarburization.
Stress Relieving
When desirable to relieve the strains of machining, heat slowly to 1050°-1250°F, allow to equalize, and then cool in still air (Strain Relieving). Â
Preheat Prior to Hardening
Warm slightly before charging into the preheat furnace, which should be operating at 1400°-1500°F.
Hardening
H13 tool steel is a steel having very high hardenability and should be hardened by cooling in still air. The use of a salt bath or controlled atmosphere furnace is desirable to minimize decarburization, and if not available, pack hardening in spent pitch coke is suggested. The temperature employed is usually 1800°-1850°F, depending on size section.
Quenching
Quench in still air or dry air blast. If complicated forms are to be hardened, an interrupted oil quench can be used. Quench part in oil and remove from bath when it just loses its color (1000°-1100°F). Finish cooling to below 150°-125°F in air, then temper immediately.
Tempering
Tempering practice may vary with size and application, but is usually performed in the range of maximum secondary hardness or higher. Double tempering is recommended. The results below is H13 that was air quenched from 1800°F and tempered for 4 hours at various temperatures. The results may be used as a guide, keeping in mind that parts of heavy section or mass may be several points lower in hardness.