Aluminum alloy 6082 and 6061-T4 are two different grades of aluminum alloys with distinct properties and applications:
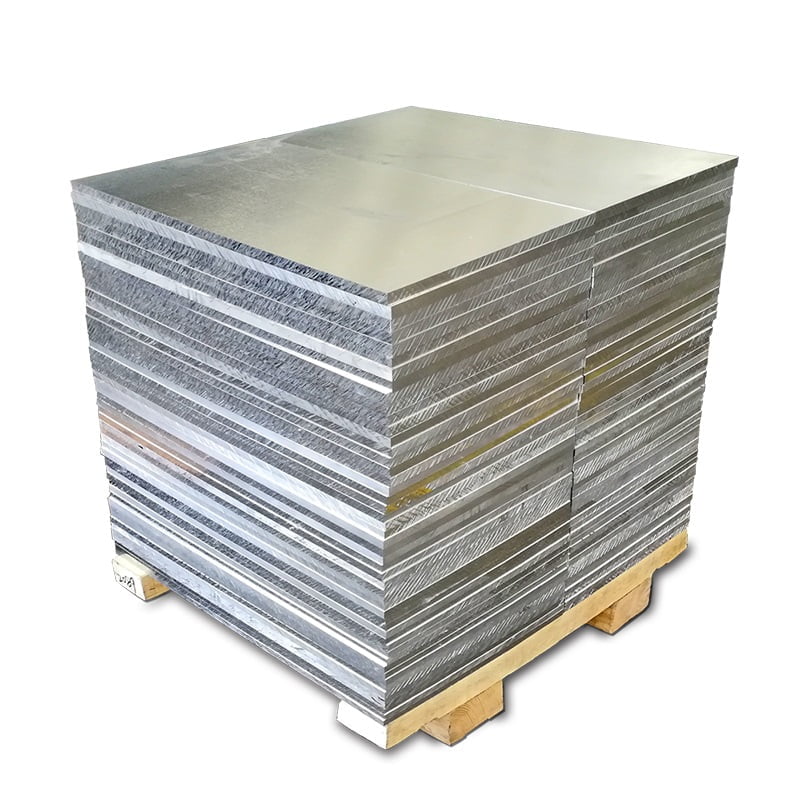
- Chemical Composition:
- 6082 Aluminum Alloy: Primarily alloyed with magnesium and silicon. Typical composition includes 0.7%-1.3% magnesium, 0.6%-1.2% silicon, and smaller amounts of copper, manganese, chromium, and titanium.
- 6061-T4 Aluminum Alloy: Alloyed with magnesium and silicon as well. It typically contains 0.8%-1.2% magnesium, 0.4%-0.8% silicon, and smaller amounts of copper, chromium, zinc, iron, and titanium.
- Temper Condition:
- 6082: Aluminum alloy 6082 is typically supplied in the T6 temper (solution heat-treated and artificially aged), which provides excellent mechanical properties. It is one of the more commonly used alloys in the 6000 series.
- 6061-T4: The designation “T4” indicates the temper condition, where the aluminum alloy has been solution heat-treated and naturally aged. It is softer than T6 but still provides good strength and formability.
- Properties:
- 6082: Offers good machinability, excellent corrosion resistance (particularly in marine environments), and good weldability. It has higher strength than 6061-T4 in the T4 condition.
- 6061-T4: Provides good machinability and weldability. In the T4 temper, it has moderate strength and good formability, making it suitable for various structural applications.
- Applications:
- 6082: Commonly used in structural applications where high strength, excellent corrosion resistance, and good machinability are required. Applications include structural components in marine and transportation industries, as well as in architectural applications.
- 6061-T4: Used in applications where moderate strength, good formability, and weldability are needed. Typical applications include aircraft and aerospace components, marine fittings, bicycle frames, and general structural components.
In summary, while both aluminum alloy 6082 and 6061-T4 share similarities in their alloying elements (magnesium and silicon) and general properties, they differ in their specific compositions, temper conditions, strengths, and applications. Choosing between them depends on the specific requirements of the application, such as strength, formability, machinability, and corrosion resistance.