Aluminum alloys 6061 and 6063 are both popular choices for various applications due to their excellent mechanical properties, versatility, and relatively low cost. Here are the main differences between these two alloys:
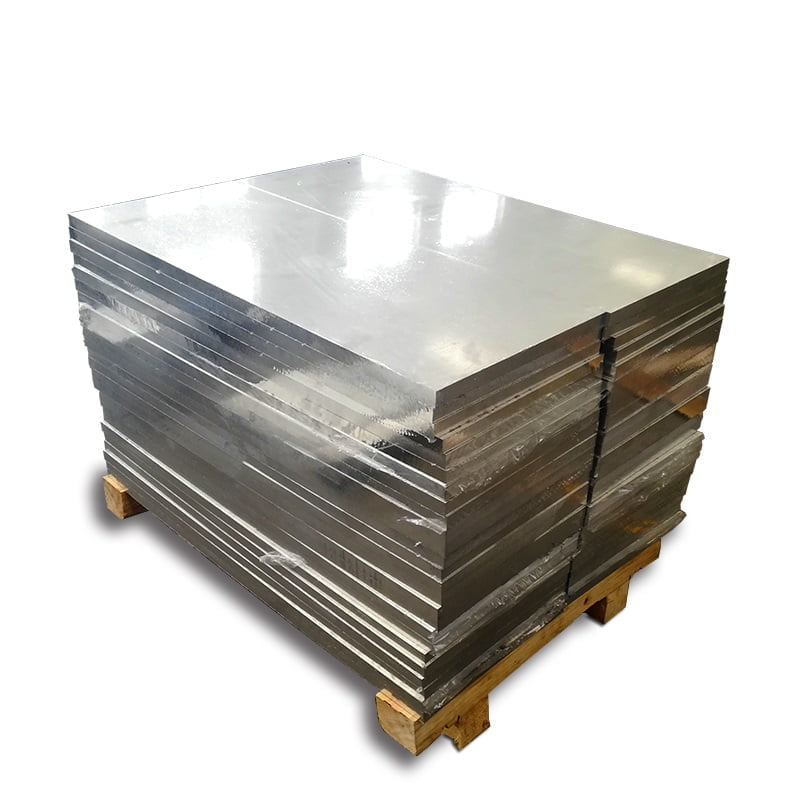
- Chemical Composition:
- 6061 Aluminum Alloy: Contains magnesium (Mg) and silicon (Si) as its major alloying elements. Typical composition ranges are 0.4%-1.0% Mg, 0.15%-0.4% Si, and smaller amounts of copper (Cu), chromium (Cr), zinc (Zn), iron (Fe), and titanium (Ti).
- 6063 Aluminum Alloy: Also contains magnesium and silicon as its major alloying elements. Typical composition ranges are 0.45%-0.9% Mg, 0.2%-0.6% Si, and smaller amounts of Cu, Fe, Mn, and Ti.
- Properties:
- 6061: Offers higher strength and toughness compared to 6063. It has good machinability and excellent corrosion resistance, making it suitable for structural applications where high strength is required.
- 6063: Is generally softer and more formable than 6061. It has better finishing characteristics, such as anodizing or painting, due to its smoother surface finish after extrusion. 6063 is commonly used for architectural applications and in applications requiring good formability and surface finish.
- Applications:
- 6061: Widely used in structural applications, such as aircraft and aerospace components, marine fittings, bicycle frames, automotive parts, and general structural components.
- 6063: Commonly used in architectural applications for window frames, door frames, roofs, and various trim components. It is also used in piping, tubing, and other applications where its good formability and smooth surface finish are advantageous.
- Temper Conditions:
- Both alloys can be supplied in various temper conditions (T6, T4, etc.), which affect their mechanical properties. T6 temper, for example, denotes solution heat-treated and artificially aged condition, providing the highest strength.
In summary, while both 6061 and 6063 aluminum alloys share some similarities in their alloying elements, they differ significantly in terms of strength, formability, and specific applications. Choosing between them depends on the specific requirements of the application, such as mechanical properties needed, formability requirements, and surface finish considerations.