Легированная сталь 42CrMo
Сталь 42CrMo по классификации материалов относится к легированным конструкционным сталям. Обладает хорошими механическими свойствами и удобоукладываемостью. Он широко используется. Есть в основном два типа материалов, пластины и круглые прутки. Его комплексная производительность лучше, чем у 40cr, что было признано в отрасли.
- Китайское название: 42 хромомолибдена
- Иностранное название: 42CrMo
- Псевдоним: 42CrMo4
- Исполнительный стандарт: национальный стандарт GB
- Происхождение: Китай
- Классификация: Легированная конструкционная сталь
- Уровень: Премиум продукт
- Спецификация: Плита, круглый стержень
Обзор 42CrMo
Сталь 42CrMo относится к сверхвысокопрочной стали с высокой прочностью и ударной вязкостью, хорошей прокаливаемостью, отсутствием явной отпускной хрупкости, высоким пределом выносливости и многократной ударопрочностью после закалки и отпуска, а также хорошей ударной вязкостью при низких температурах. Сталь 42CrMo подходит для изготовления пластиковых форм больших и средних размеров, требующих определенной прочности и ударной вязкости.
Химический состав 42CrMo
- Углерод С: 0,38~0,45%
- Кремний Si: 0,17~0,37%
- Марганец Мн: 0,50~0,80%
- Сера S: допустимое остаточное содержание ≤0,035%
- Фосфор P: допустимое остаточное содержание ≤0,035%
- Хром Кр: 0,90~1,20%
- Никель Ni: допустимое остаточное содержание ≤0,30%
- Медь Cu: допустимое остаточное содержание ≤0,30%
- Молибден Мо: 0,15~0,25%
42CrMo механический Характеристики
- Твердость: отожженный, 147~241HB, 42CrMo
- Механические свойства 42CrMo:
- Прочность на растяжение σb (МПа): ≥1080 (110)
- Предел текучести σs (МПа): ≥930(95)
- Удлинение δ5 (%): ≥12
- Уменьшение площади ψ (%): ≥45
- Энергия удара Akv (Дж): ≥63
- Значение ударной вязкости αkv (Дж/см2): ≥78(8)
- Твердость: ≤217HB
Чтобы увеличить срок службы пресс-формы более чем до 800 000 раз, предварительно закаленная сталь может быть реализована методом закалки и низкотемпературного отпуска. При закалке предварительно нагревают до 500-600°С в течение 2-4 часов, затем выдерживают при 850-880°С определенное время (не менее 2 часов), после чего помещают в масло и охлаждают до 50-100°С. ° C и воздушное охлаждение, твердость может достигать 50 после закалки -52HRC, во избежание растрескивания следует немедленно провести низкотемпературный отпуск при 200 ° C. После отпуска твердость может поддерживаться выше 48HRC.
Лечение инфильтрации ванадием в соляной ванне
42CrMo Закалка
Программа | Температура закалки / ° C | Характер | |||
Использовать | Температура нагрева / ° C | Середина | Твердость HRC | ||
(1) (2) (3) | 1020~1040 | Снятие стресса Снимите напряжение и уменьшите твердость Снимите напряжение и уменьшите твердость | 150~170 200~275 400~425 | Масло или нитрат - - | 61~63 57~59 55~57 |
(4) (5) (6) | 1115~1130 | Снятие напряжения и образование вторичной закалки Снятие напряжения и образование вторичной закалки Снятие напряжения и образование вторичной закалки | 510~520°C многократный отпуск -78°C холодная обработка Однократный отпуск при 510 ~ 520 ° C Холодная обработка -78°C плюс однократный отпуск 510~520°C, затем холодная обработка -78°C | - - - | 60~61 60~61 61~6 |
42CrMo закалка
Программа | Первый предварительный нагрев / ° C | Второй предварительный нагрев / ° C | Температура закалки / ° C | остыть | Остудить в среде | Средняя температура / ° C | Средняя | твердость (КПЧ) |
(1) (2) (3) (4) (5) | 550~660 | 840~860 | 950~1000 1020~1040 1020~1040 1115~1130 1115~1130 | масло масло Расплавленный нитрат масло Расплавленный нитрат | 20~60 20~60 400~550 20~60 400~450 | До комнатной температуры До температуры масла 5~10мин До температуры масла 5~10мин | Воздушное охлаждение Воздушное охлаждение Воздушное охлаждение Воздушное охлаждение Воздушное охлаждение | 58~62 62~63 62~63 42~50 42~50 |
Соответствующая оценка
- Россия ГОСТ 38ХМ,
- американский AISI 4140/4142,
- Британский БС 708М40/708А42/709М40,
- французский NF 40CD4/42CD4,
- Немецкий DIN 41CrMo4/42CrMo4,
- Япония JIS SCM4,
- Международный ИСО 683/1 3
Спецификация закалки
Общие характеристики закалки и отпуска: температура закалки 1000~1050°C, закалка маслом или закалкой газом, твердость ≥60HRC; температура отпуска 160~180°C, время отпуска 2 часа или температура отпуска 325~375°C, время отпуска 2~3 раза.
Физические свойства
- Температура критической точки (приблизительное значение): Ac1=730°C, Ac3=800°C, Ms=310°C.
- Коэффициент линейного расширения: температура 20~100°C/20~200°C/20~300°C/20~400°C/20~500°C/20~600°C,
- Коэффициент линейного расширения: 11,1×10K/12,1×10K/12,9×10K/13,5×10K/13,9×10K14,1×10K.
- Модуль упругости: температура 20°C/300°C/400°C/500°C/600°C,
- Модуль упругости 210000 МПа / 185000 МПа / 175000 МПа / 165000 МПа / 15500 МПа
Спецификация процесса
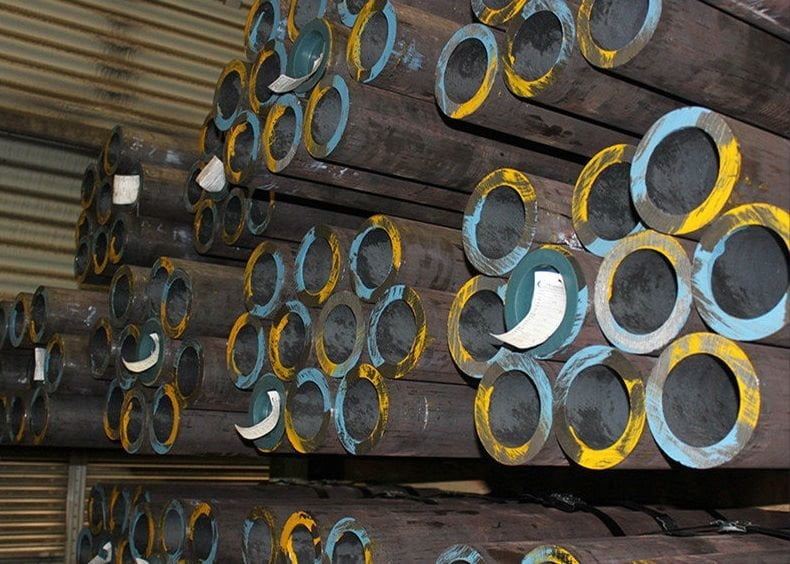
Типичные примеры применения